Existen diferentes motivos para la inadaptación en lentes progresivas. El objetivo de este artículo es determinar el origen de estas.
Hay cinco elementos principales a considerar frente a una inadaptación:
- Usuario
- Montura
- Lentes
- Biselado
- Diseño
Es importante disponer de una lista de las diferentes comprobaciones que deben tenerse en cuenta en cada uno de los diferentes elementos mencionados.
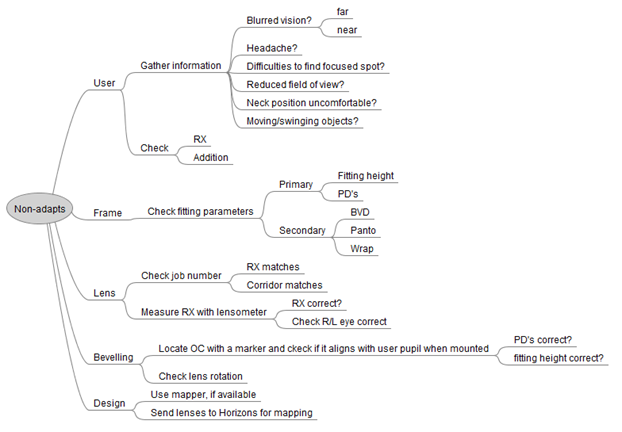
Imagen 1: pasos en las comprobaciones de inadaptación.
Para cada elemento, hay algunos puntos clave a considerar para lograr el mejor rendimiento de la lente y evitar las inadaptaciones.
- USUARIO
En primer lugar, el profesional debe recopilar la máxima información sobre cada usuario concreto para comprender qué problemas está experimentando.
En concreto, entender los problemas visuales de lejos, intermedios y de cerca, si tiene visión borrosa, sensación de mareo u otra sintomatología visual.
Cuando el profesional comprende adecuadamente los problemas del usuario, puede seguir el flujo de trabajo adecuado para encontrar la causa principal de su inadaptación.
- MONTURA
En algunos casos, la forma de la montura puede ser la causa de la inadaptación. A veces, el usuario lleva unas lentes de uso específico que requieren unos aspectos técnicos que no son posibles con algún tipo de montura. Además, aunque la selección de la montura sea adecuada, puede ser que los datos de montaje o centrado no lo sean.
En relación con los parámetros de montaje, es importante:
- Comprobar la posición de uso de los parámetros de desgaste, si se proporcionan.
Es importante garantizar que las lentes estén en la posición correcta frente al ojo del usuario. Hay seis parámetros diferentes a considerar cuando se toma en consideración la posición de uso.
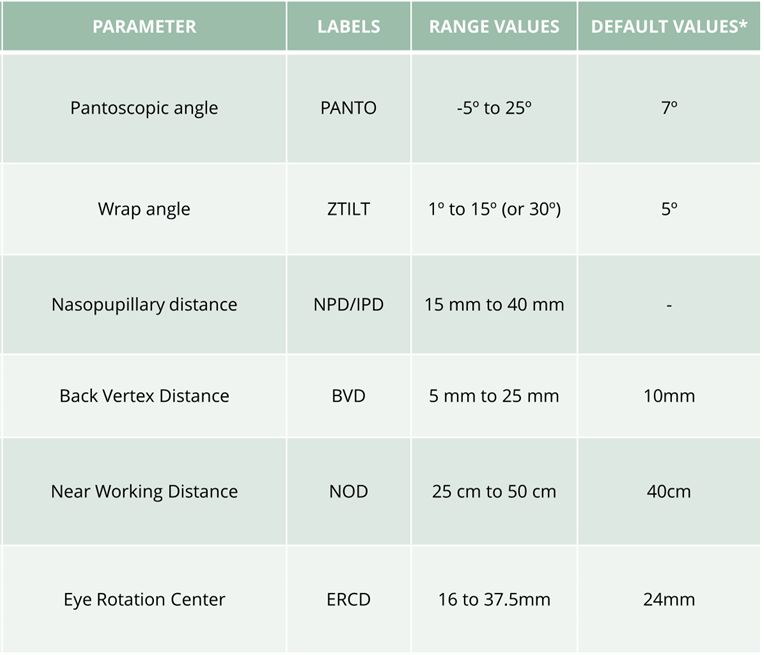
Imagen 2: parámetros de posición de desgaste.
2. Comprobar la distancia pupilar.
Existen diferentes comprobaciones a seguir a la hora de validar la distancia pupilar:
- Marca con tinta las marcas de grabado utilizando el diseño proporcionado por el proveedor.
- Coloca las lentes en la regla. La zona nasal en la distancia del medio puente y la medida de la cruz de montaje es la que se debe medir para obtener la medida de las distancias pupilares.
También es posible colocar las lentes sobre la regla, dejando el cero en medio de ambas lentes. La distancia pupilar es el valor resultante sumando la mitad de la distancia del puente.
3. Verificar la medida de la cruz de montaje.
Valida la medida de la cruz de montaje. La altura de montaje se utiliza para definir la posición vertical de la cruz de montaje, por lo que para determinar la medida de la cruz de montaje es necesario colocar las lentes en la regla. Pon a cero la cruz de montaje y comprueba si la medida de la cruz de montaje coincide con la de la ficha. Después, verifica la posición horizontal colocando las monturas en el gráfico. Más de cinco grados pueden resultar incómodos para el usuario.
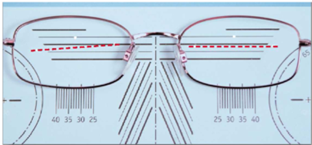
Imagen 3: verificación de la cruz de montaje.
- LENTES
Hay cuatro aspectos diferentes a tener en cuenta al comprobar las lentes:
- Prescripción de las lentes
- Lentes de fabricación
- Corredor asignado
- Filosofía progresiva diferente a la utilizada anteriormente
La primera comprobación que debe hacer el profesional es verificar la prescripción del usuario, el valor de la suma y el valor de la longitud del corredor.
El profesional debe asegurarse con un focimetro de que las lentes definitivas tienen la graduación deseada.
Con el fin de evaluar la tolerancia de potencia, existen diferentes tablas que muestran la desviación de potencia máxima a distancia, la desviación de potencia cilíndrica y la desviación de potencia de adición.
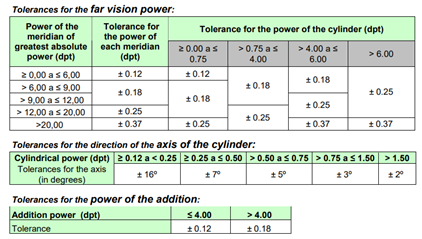
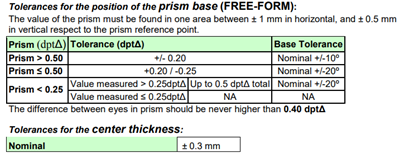
Imagen 4: tolerancias de fabricación.
Además, es importante verificar que las lentes hayan sido fabricadas correctamente. La importancia de estos patrones de error se puede cuantificar objetivamente mediante la función Go/NoGo del A&R Dual LensMapper.
Además, un corredor incorrecto (demasiado corto o demasiado largo) puede causar molestias a los usuarios de lentes progresivas. Para evitar que las lentes no se adapten, a la hora de elegir el corredor ideal hay que tener en cuenta los siguientes aspectos:
- 18 mm como valor de corredor predeterminado.
- El diseño progresivo anterior y el valor del corredor anterior: cada diseño de lentes tiene su propia definición de corredor y, para emparejar dos diseños diferentes de dos diseñadores distintos, es obligatorio asegurarse de que la equivalencia de corredor es la adecuada para lograr el mejor rendimiento visual para el usuario final.
- La prescripción anterior.
Como no existe una definición clara de la longitud del corredor en la norma VCA, cada fabricante de lentes tiene una definición diferente.
Visión de HORIZONS sobre el corredor: se mide desde la cruz de montaje hasta la parte inferior del círculo de la zona cercana que está 2 mm por debajo del PNR que coincide con la altura mínima del accesorio.
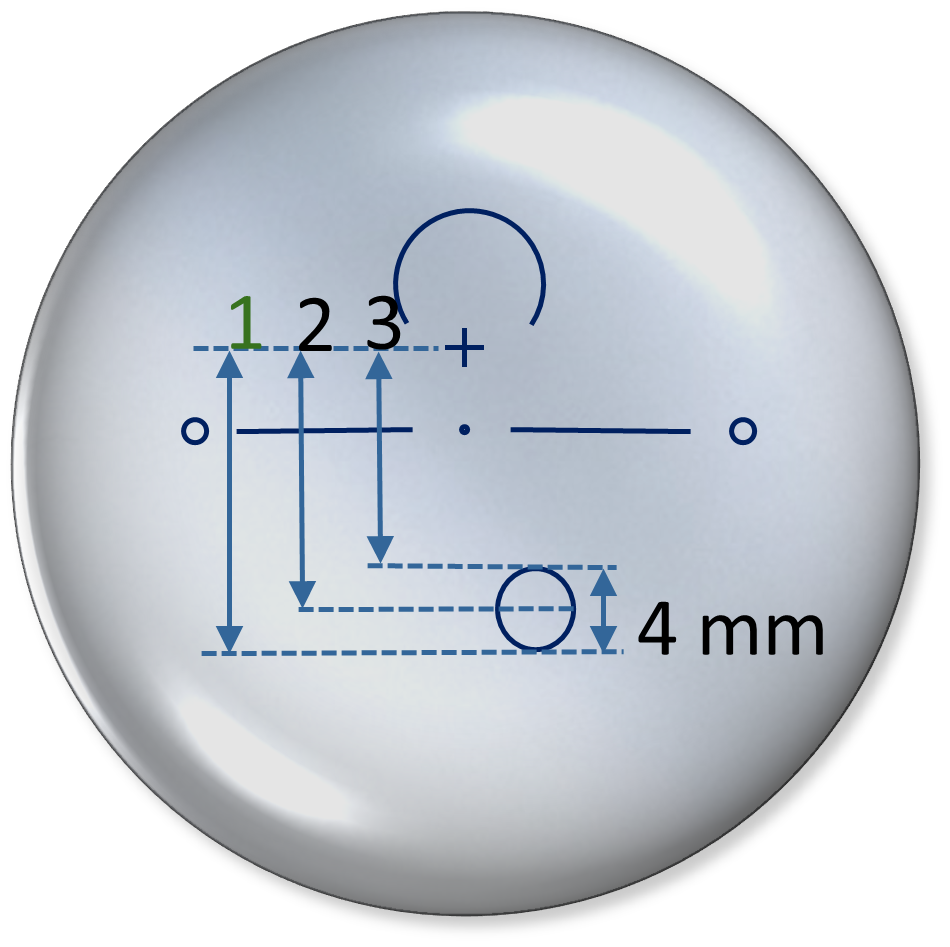
Parámetros del corredor para Horizons:
1: de 14 mm a 20 mm
2: otra definición de «corredor», de 12 mm a 18 mm
3: otra definición de «corredor», de 10 mm a 16 mm
Imagen 5: correspondencia del corredor
Comprueba si hay rotaciones.
En caso de cualquier rotación en la montura, el usuario que lleve lentes progresivas de adición no encontrará el corredor ni la zona cercana de la lente. A continuación, mostramos algunos ejemplos de colocación incorrecta de las lentes progresivas de adición y la posición correcta que debe tener la montura:
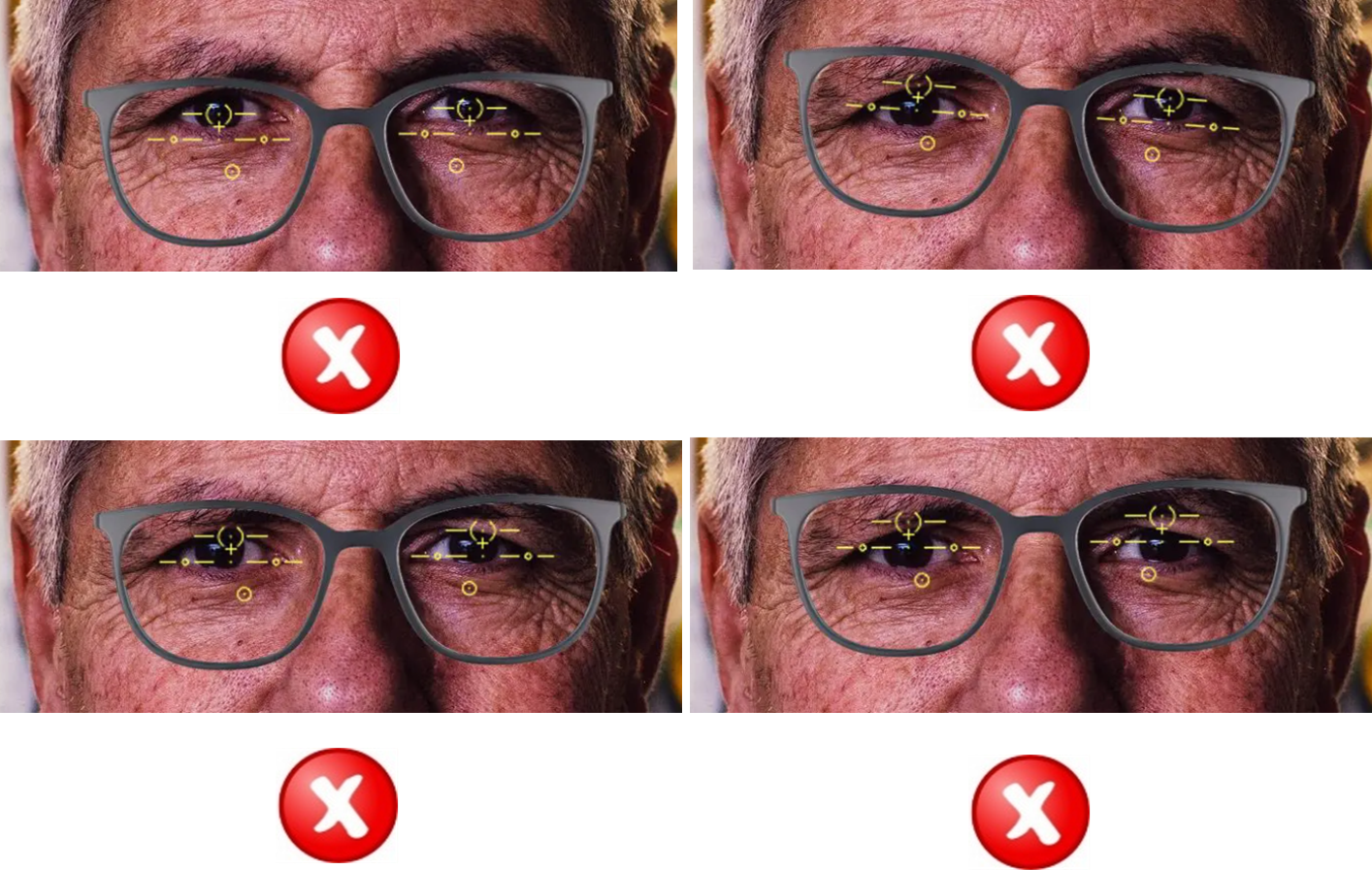
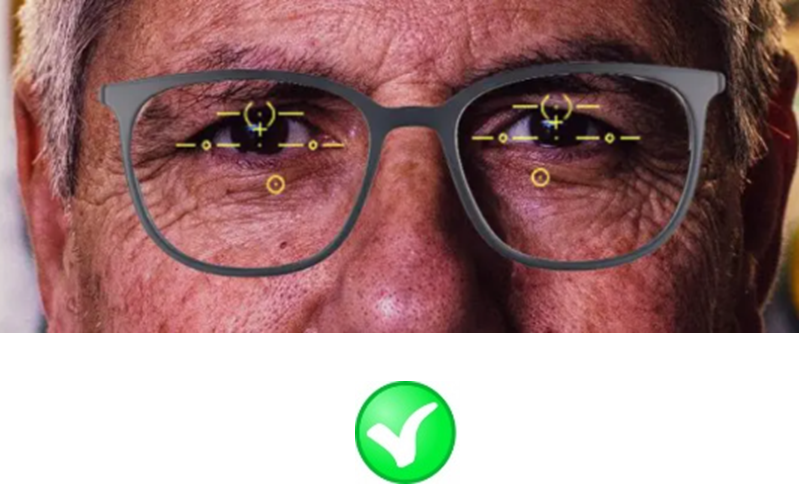
Imagen 6: centrado PAL.
- DISEÑO
Como se ha mencionado, es crucial considerar el diseño progresivo anterior para lograr un rendimiento visual similar o mejor. Si el usuario llevaba un diseño suave y ahora un diseño duro, puede ser un caso de inadaptación ya que los campos visuales y la percepción visual son muy diferentes en ambos casos.
CONCLUSIÓN
Para lograr la mejor adaptación, se deben tener en cuenta los elementos descritos.
Conseguir la mejor adaptación significa proporcionar la mejor calidad al óptico, disminuir el coste y el tiempo para el laboratorio y mejorar el rendimiento visual para el usuario final y ofrecer confianza en el producto.